Press Brake vs. Finger Brake: Key Differences
I. Introduction
In contemporary sheet metal fabrication projects, metal bending machines such as hydraulic press brakes, servo-electro press brakes, and CNC press brakes are widely used. However, some special-purpose bending machines, such as finger brakes, remain popular in the metalworking industry.
Although the functions of the press brake are similar to those of the finger brake, their operating principles and bending methods are quite different from each other. Today, I will show you the differences between a press brake and a finger brake. First, let's watch the video for understanding:
II. What Is Finger Brake?
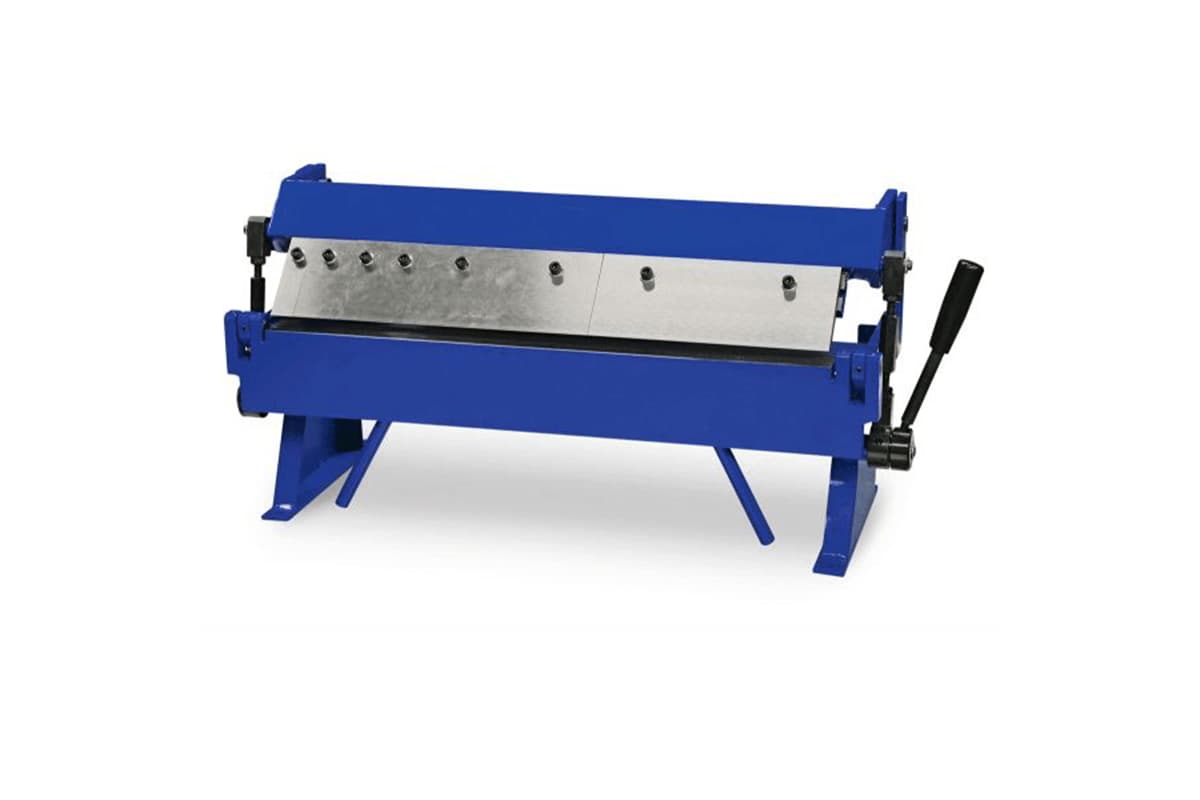
Box and pan brakes are commonly used to bend thin metal plates made of high-tensile strength materials, such as stainless steel, aluminum, and other alloys. These brakes, also known as finger brakes, work by using a clamping rod with removable steel fingers of varying widths.
Finger brakes are mainly utilized for forming objects like boxes and pans. The fingers are secured in place by thumbscrews, and any unused fingers can be removed before bending. Tightening all thumbscrews and securing the fingers before using pan and box brake to avoid any unwanted bending or deformation is crucial.
In conclusion, box and pan brakes, also known as finger brakes, are specifically designed to bend thin metal plates into objects like boxes and pans by using removable steel fingers and clamping rods.
III. What Is Press Brake?
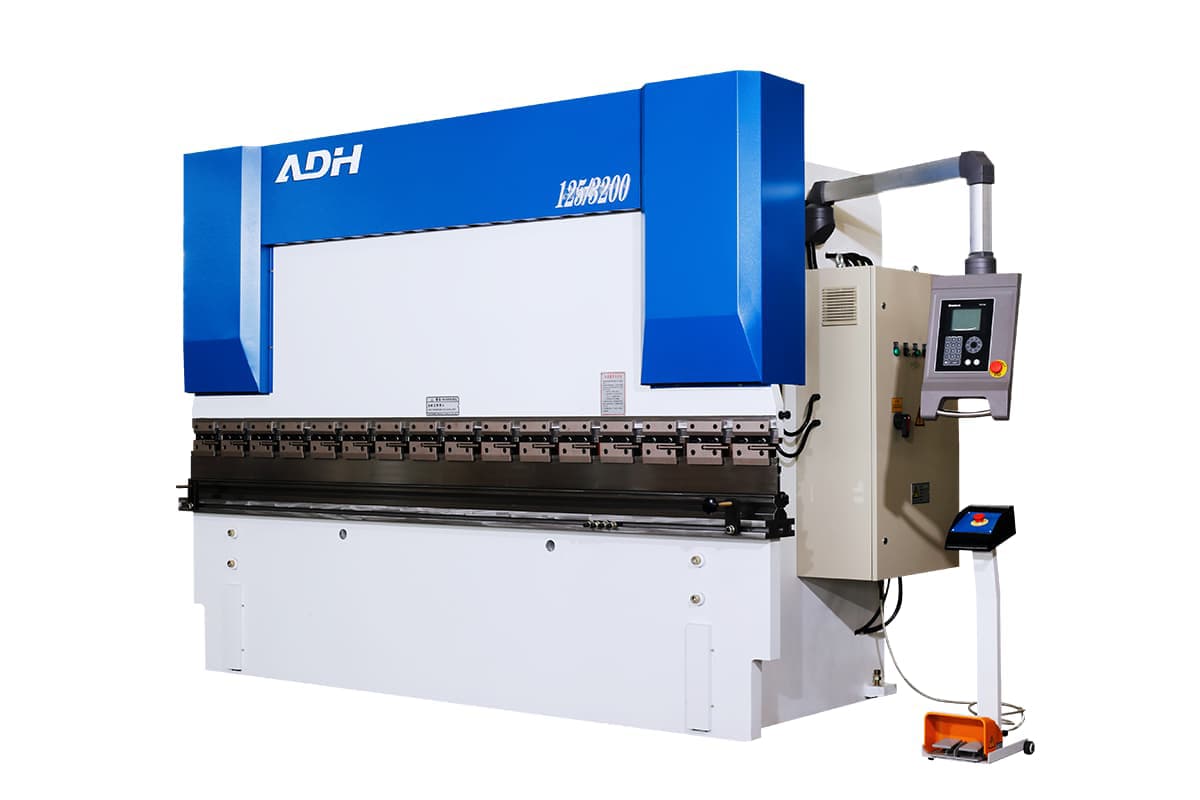
A press brake is a machine commonly utilized in the sheet metal industry for the purpose of bending sheet metal. The history of bending machines dates back to the simple cornice brake and has evolved over time to the hydraulic press brake and eventually the CNC press brake.
The CNC (Computer Numerical Control) press brake is known for its accuracy and efficiency in bending metal sheets, achieved through programming. These modern press brakes equipped with CNC are versatile and can achieve complex sheet metal bending, making them widely utilized in industries such as automotive, construction, and aviation.
In the world of metal bending, the press brake can handle sheet metal work, has varying bending capacities, and is capable of bending plates of varying lengths and thicknesses.
IV. What Are the Differences: Press Brake vs Finger Brake
1. Functions
(1) Finger Brake
The finger brake is predominantly utilized for creating boxes, pans, channels, angles, and other similar objects of varying depths and sizes. It also has the capability of creating hemming, processing both open and closed hems and even lighter gauge hems.
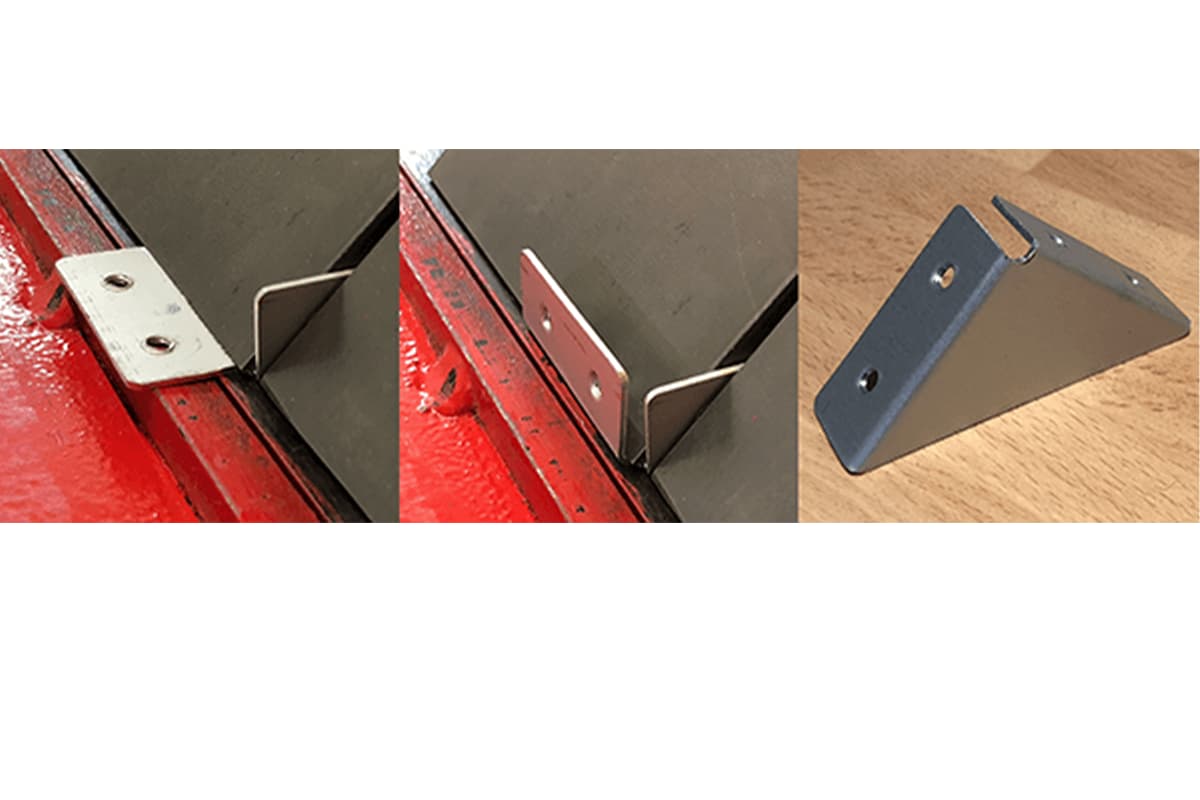
The sheet metal finger brake bends the metal to over 130 degrees and then flattens the hem using the apron and presses it firmly against the top of the clamping rod. It is mainly utilized for bending simple workpieces or for prototype design and production.
This sheet metal brake can also be utilized for one-time sheet metal forming for automobile bodies and for HVAC workpieces, as it is capable of performing small, complex angle bends quickly.
(2) Press Brake
In comparison, the press brake offers a more advanced range of functions than the finger brake. There are various types of press brakes, all of which consist of a frame, workbench, ram, tooling, and driving device.
The driving device of the press brake can be manual, mechanical, hydraulic system, servo motor, or pneumatic, resulting in different bending forces exerted on the workpiece. This leads to a tonnage range for the press brake of 40 tons to 1000 tons.
This ability to exert varying forces enables the press brake to bend plates of varying thicknesses without damaging the machine. The length of the press brake's worktable determines the length of the sheet that can be bent.
A smaller press brake can bend shorter plates while a tandem press brake is designed to bend larger workpieces. The press brake's tooling consists of a group of dies with various angles and shapes, including punches (right angle, acute angle, obtuse angle, gooseneck) and dies (U-shape, V-shape, single mode, double mode).
CNC press brakes are equipped with controllers that allow for accurate real-time control of bending angles and times. The backgauge system of the press brake features multiple axes that ensure precise bending accuracy. The complex functionality of the press brake enables it to produce workpieces of diverse and intricate shapes.
2. Structures and Working Principles
(1) Finger Brake
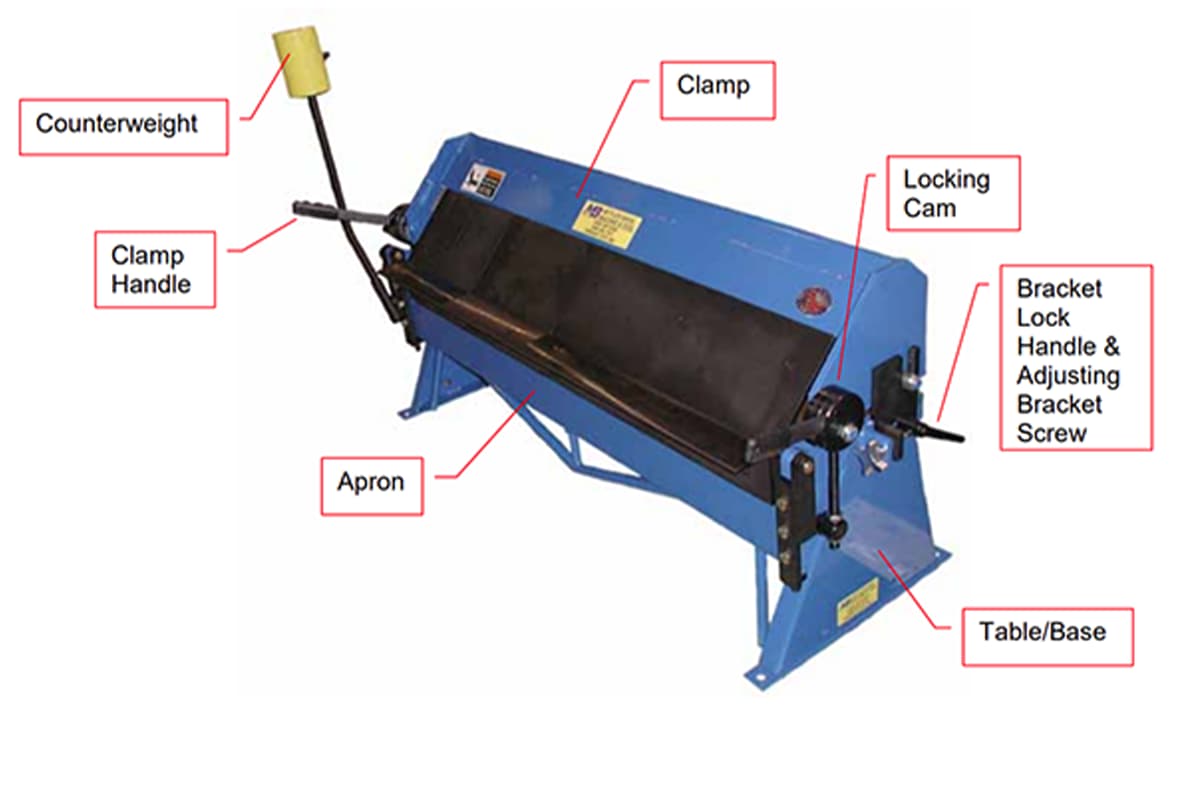
The finger brake is mainly composed of a frame, a forming rod, and a clamping mechanism and is manually operated. The body is made of heavy steel and the steel plate structure ensures that the bending angle will not be affected, even under full load.
The machine also features super-heavy truss rods and supports for minimal deflection and powerful operation. The finger brake is equipped with an extended handle and an apron stop for repeated bending and a replaceable bushing to mitigate wear.
The key difference between the finger brake and the press brake is that its clamping rod is equipped with removable fingers. These fingers can be disassembled or rearranged to bend a metal plate or modify a part of the formed workpiece.
The finger brake is manually operated by the operator and can be operated by one or two operators, depending on the size of the workpiece. To complete the forming of boxes, pans, and other objects, the workpiece can be fixed using screws, rivets, welding, or other fixing processes.
To bend a sheet of metal, the clamping rod is opened by pushing the clamp handle to the back of the machine. The metal sheet is placed in the opening between the clamp finger and the work table, and the grip handle is pulled forward to fix the material in place. The baffle is then pulled up and the metal sheet is bent to the desired angle.
(2) Press Brake
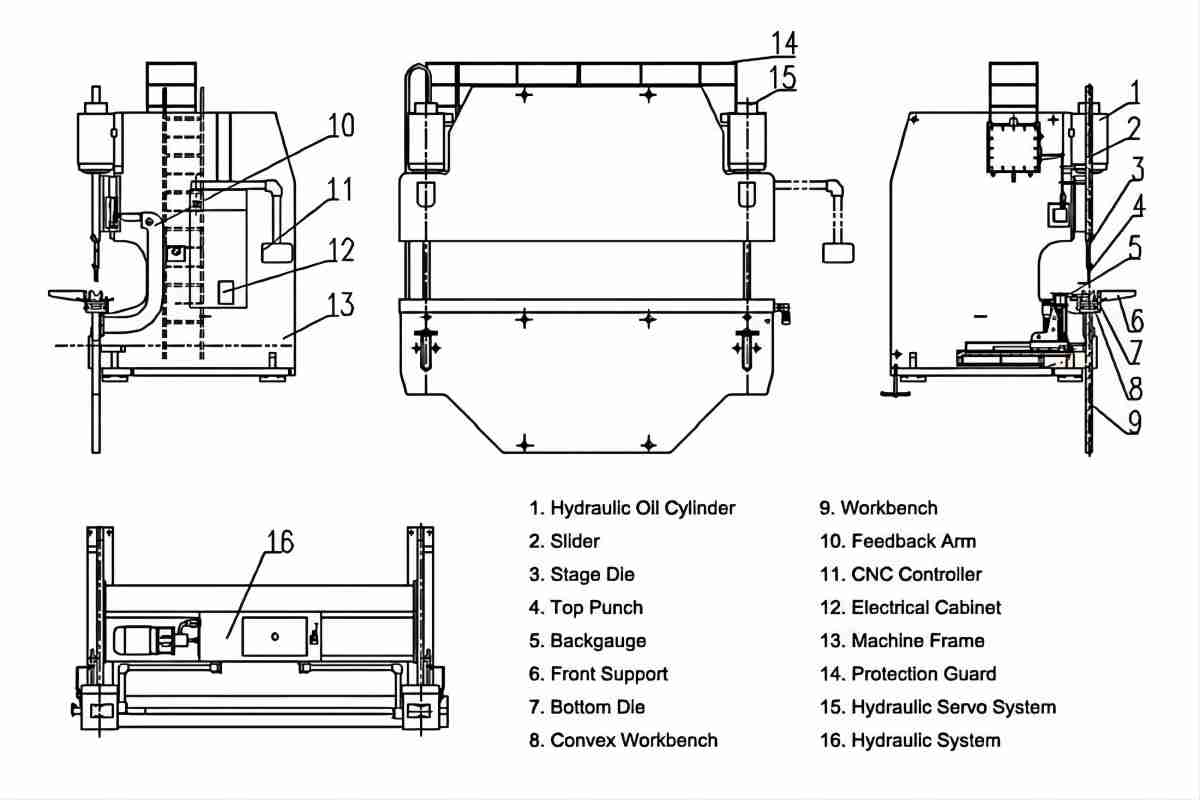
Although there are many types of press brakes, their structures are generally similar and consist of a frame, worktable, ram, toolings, electrical control box, and power system. The CNC press brake is equipped with additional features, such as a controller, backgauge, light curtain protection, and crowning device.
To use the press brake, the sheet metal must be placed on the worktable and secured, and then the machine is started. The upper die presses the metal sheet onto the lower die, driven by the ram, and then returns, completing a stroke.
The press brake operates through the combined efforts of the controller and the operator, performing repeated bending. A variety of toolings can be interchanged to produce workpieces of different shapes and designs.
3. Press Brake vs. Finger Brake Comparison Table
Feature | Press Brake | Finger Brake |
Maximum Bending Force | Up to 3000 tons | Up to 50 tons |
Working Table Length | 4 feet to 40 feet | 2 feet to 12 feet |
Maximum Sheet Thickness | Up to 1 inch (25.4 mm) | Up to 0.25 inch (6.35 mm) |
Bending Angle Range | 0° to 180° | 0° to 135° |
Material Compatibility | Steel, Aluminum, Stainless Steel,etc. | Steel, Aluminum, Copper, etc. |
Control System | CNC, Manual, Hydraulic | Manual, Pneumatic |
Accuracy | ±0.01mm | ±0.1 mm |
Speed | Up to 20 bends per minute | Up to 10 bends per minute |
Tooling Options | Wide range of dies and punches | Adjustable fingers for custom bends |
Power Requirement | 220V/380V,3-phase | 110V/220V, single-phase |
Weight | 1 ton to 50 tons | 200 kg to 2 tons |
Application Scenarios | Large-scale manufacturing, automotive parts, heavy machinery components | Custom metal fabrication, small batch production, repair shops |
Cost | Higher initial investment and maintenance costs | Lower initial investment and maintenance costs |
Flexibility | High, suitable for complex and high-precision bending | High, suitable for frequent setup changes and custom bends |
Portability | Heavier, usually fixed installation | Lighter, easier to move and set up |
4. Performance Comparison Between Press Brake and Finger Brake
(1) Press Brake
- High Bending Force: Capable of handling very thick and tough materials, making it suitable for heavy-duty applications such as automotive and aerospace industries.
- Precision and Accuracy: With CNC control systems, press brakes offer high precision and repeatability, essential for complex and high-volume production.
- Versatility: Can perform a wide range of bends and shapes with various tooling options, making it ideal for custom and intricate designs.
- Speed: Faster bending speeds make it suitable for high-volume production runs.
- Material Range: Can handle a wide variety of materials, including high-strength steels and alloys.
(2) Finger Brake
- Flexibility: Finger brakes are ideal for creating custom bends and box shapes due to their adjustable fingers, making them perfect for small-scale and prototype work.
- Ease of Use: Generally simpler to operate with manual or pneumatic controls, suitable for workshops and small manufacturing units.
- Cost-Effective: Lower initial investment and maintenance costs compared to press brakes, making it accessible for smaller businesses.
- Portability: Lighter and more compact, easier to move and set up in different locations.
- Material Limitations: Best suited for thinner materials and less demanding applications, such as HVAC ductwork and light metal fabrication.
5. Application Scenarios
- Press Brake: Best for large-scale manufacturing, automotive parts, heavy machinery components, and any application requiring high precision and strength.
- Finger Brake: Ideal for custom metalwork, small batch production, repair shops, and applications requiring frequent setup changes and custom bends.
6. User Case Studies
(1) Press Brake User Case Study
- Company: XYZ Manufacturing
- Industry: Heavy Machinery
- Challenge: XYZ Manufacturing needed to produce large, high-strength components for their heavy machinery products. The components required precise bends and high repeatability.
- Solution: XYZ Manufacturing invested in a CNC press brake with advanced control systems. The press brake's high bending force and precision allowed them to produce the required components with consistent quality.
- Outcome: The company saw a significant improvement in production efficiency and product quality. The press brake's versatility also enabled them to expand their product range and take on more complex projects.
(2) Finger Brake User Case Study
- Company: ABC Metalworks
- Industry: Custom Metal Fabrication
- Challenge: ABC Metalworks needed a flexible solution for creating custom metal parts and prototypes for their clients. They required a machine that could handle frequent setup changes and produce precise bends.
- Solution: ABC Metalworks purchased a finger brake with adjustable fingers. The finger brake's ease of use and flexibility allowed them to quickly switch between different projects and create custom bends as needed.
- Outcome: The company experienced increased customer satisfaction due to their ability to deliver high-quality, custom metal parts on time. The finger brake's cost-effectiveness also helped them maintain competitive pricing.
V. What Is Box and Pan Brake?
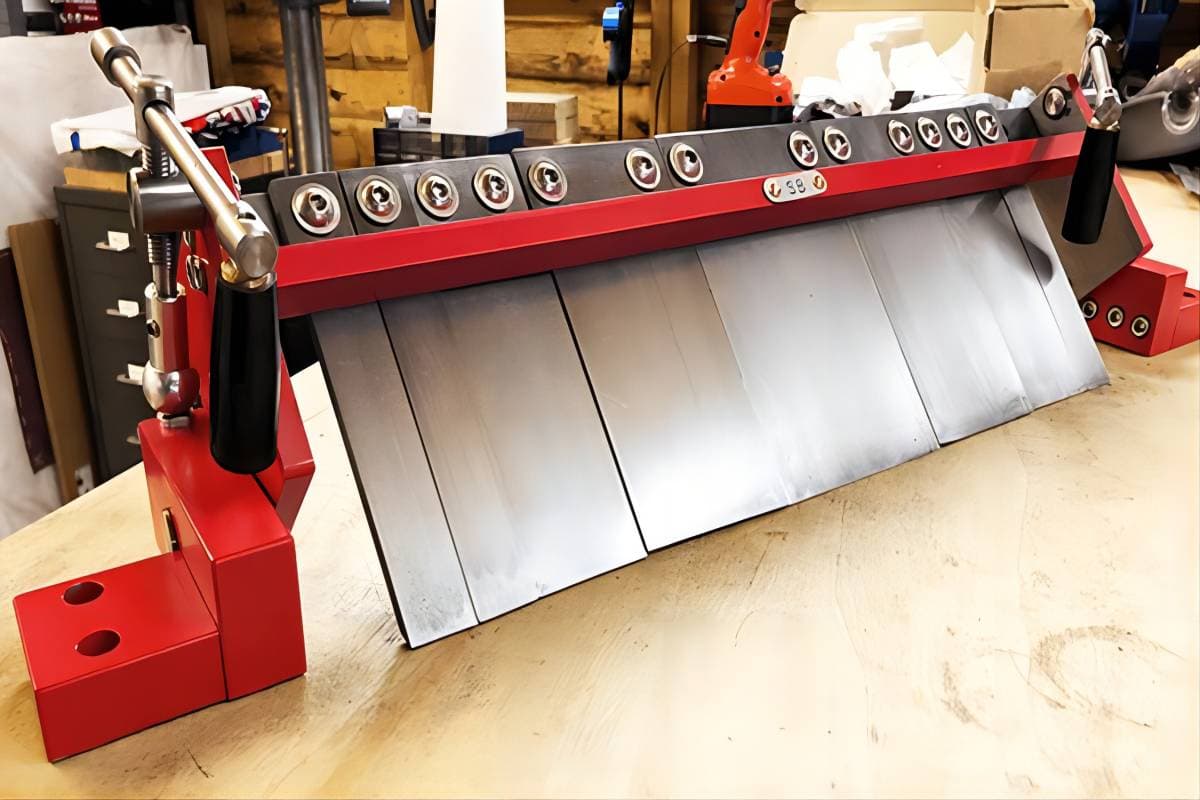
This paper focuses on box and pan brakes, also known as finger brakes, which are a type of leaf brake. They are primarily used for forming boxes, pans, and other objects. This manual brake consists of a frame, a clamping rod, and steel fingers which act as clamps.
It has three interchangeable finger parts: upper, bed, and apron angle fingers. The fingers on the clamping rod are adjustable and can be disassembled and replaced. They have different angles, lengths, and radii to accommodate varying material thicknesses and positions of the rear gauge.
To use the brake, the metal sheet is fixed and the finger is adjusted to the required specifications and inner radius. The lever is then used to bend the metal sheets into desired angle.
Which Is Better? Press Brake or Finger Brake?
Firstly, the press brake technology is more advanced compared to that of the finger brake. The finger brake is primarily used for forming boxes, pans, and similar objects. Meanwhile, the press brake has multiple functions and is capable of performing various complex bending operations.
However, the cost of a press brake is significantly higher than that of a finger brake. If simple bending is all that is needed, there's no need to invest a large budget in a press brake. On the other hand, for complex and multi-functional batch bending operations, the press brake is the ideal machine.
The finger brake has a simpler operation compared to the press brake as it has fewer components and a straightforward design. However, its safety is lower than that of the press brake, so extra caution must be taken when using it.
VI. Conclusion
This article highlights the comparison between the press brake and finger brake and outlines their respective strengths and weaknesses. Despite advancements in press brake technology, finger brakes continue to be widely utilized in the sheet metal industry.
Consider choosing an ADH press brake if your company requires a high-performance press brake to enhance productivity. My company, ADH Machine Tool, specializes in manufacturing machines for the sheet metal industry. For further information, please feel free to reach out to our sales team.
Automatic Quilting Sewing Machine
Cost-effective High-quality Sewing Machines,OEM-ready of Equipment,Clothing Production Machines
Sichuan Kisae sewing machine Co.,Ltd. , https://www.kisaesew.com