A Novel Method to Optimize High Precision Injection Molded Progressive Addition Lenses
Â
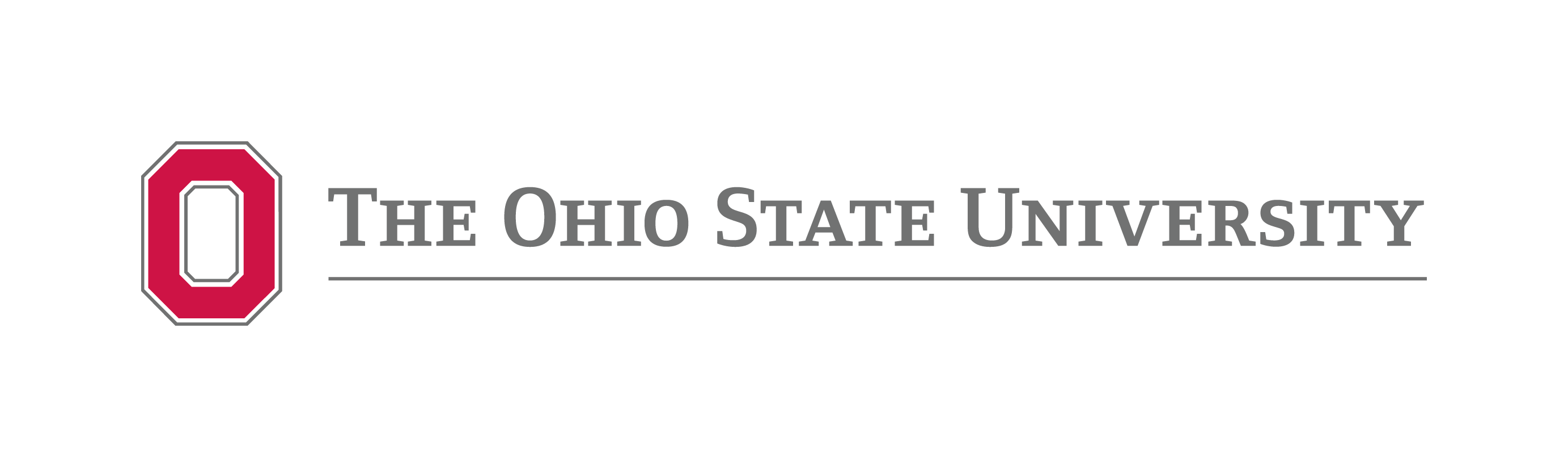
- Customer:Â The Ohio State University
- Country: USA
- Industry: Optics
- Solution: Moldex3D Advanced / Moldex3D Optics
Executive Summary
Progressive addition lenses (PALs) have been widely accepted for the compensation of presbyopia (i.e. the decline in ocular accommodation with age) over the past 60 years, and they are typically manufactured using casting process. However, manufacturing cost for the traditional methods polymer casting is high due to limited production rate. Therefore in this research, the aim is to develop a process of combining ultra-precision diamond turning and microinjection molding to create a unique low cost manufacturing process for progressive addition lenses, or PALs.
Challenges
- Part warpage and uneven refractive index distribution changed the light propagation through the lens into the eyes.
- Unfilled hole occurred for plastic coating on hybrid glass-polymer PALs and high residual stress results in crack of part inserts.Â
Solutions
The Precision Engineering Research Lab deployed injection molding simulation technology from Moldex3D to help:
- Optimize the injection molding process parameters to achieve better quality and compensate the optical aberration.
- Optimize the part design and process parameters of the plastics coating.
Moldex3D Optics helps determine the appropriate packing pressure to avoid deformation problems
Case Study
To address the above optical challenges, The Precision Engineering Research Lab of OSU developed a method of determining the optical aberrations of the injection molded PALs using the Optics Module of Moldex3D. This method involves reconstructing the wavefront pattern in the presence of uneven refractive index distribution and surface warpage using a finite element method. In addition to numerical modeling, a measurement system based on a Shack-Hartmann wavefront sensor was used to verify the modeling results. Besides, the flow pattern of polymer melt can also be predict by Moldex3D to coat thin plastic layer for hybrid glass-polymer PALs. The PALs were fabricated by microinjection molding under well controlled process conditions. In order to evaluate the optical performance of these PALs, a Shack-Hartmann wavefront sensor system was setup, and the measured data were stitched together to map the optical surface for the entire lens using mathematical manipulations. Besides the measurements using an optical setup, numerical modeling of the optical performance of the molded lenses was also performed. The refractive index variation and geometric deformation results obtained by Moldex3D Optics Module were exported to calculate the optical aberrations of the injection molded PALs according to wavefront optics theorem. The optical aberrations for design, simulation and measurement were compared and analyzed. Since the numerical simulation and experiment plots are in good agreement with each other, the simulation can be used to accurately predict optical aberrations of injection molded PALs. Moreover, the flow pattern of polymer melt was also accurately be predict by Moldex3D to visualize thin plastic coating for hybrid glass-polymer PALs.
The simulation results (B) showed good correlation to the wavefront sensing measurementsÂ
The simulation accurately predicts the unfilled holes formed at the center of the aperture of the
injection molded polymer lensÂ
Utilizing the simulation result obtained from Moldex3D, the optical setup is geometrically re-designed, increasing the polymer lens thickness from 0.126 mm to 0.726 mm to avoid unfilled holes
Results
This research presents a new approach to fabricate PALs using the combination of ultraprecision diamond turning and precision injection molding. This approach has wide industrialization potential due to its affordability. Also, it is demonstrated that how Moldex3D simulation analysis help understand the part geometry shrinkage and the melt front pattern resulted from injection molding process, and further optimize the part design and process parameters of the injection molded PALs.
![]() |
The greatest value of this research project is that it demonstrates how simulation can reduce the manufacturing cost and maintain the optics precision at the same time.
|
Measuring Device,Cnc Machine Touch Probe,Cnc 3D Touch Probe,Cable Alignment Device
Suzhou Loong Won Machinery Technology Co., Ltd. , https://www.loongwon.com