Machine Tool Industry Increases Sensor Requirements
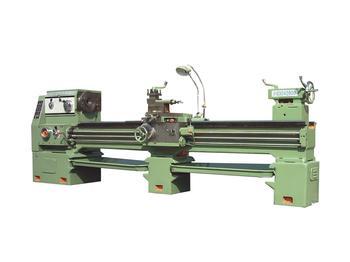
The huge automobile market will inevitably stimulate the development of the related spare parts machine tool industry. According to the “2012 Global Automobile Industry Senior Management Survey Report†published by KPMG, the number of idle cars in China reached 6 million units in 2011. It is estimated that by 2016, Idle capacity will also increase to 9 million vehicles. By then, the competition in China's passenger vehicle market will be fierce and the companies will face the survival of the fittest, while large-scale mergers and reorganizations and market adjustments will emerge.
Machine tools are the technological means of automobile production. The level of manufacture and quality of automobiles depends largely on the level of precision of the molds and machine tools. The automotive and parts industry is the largest and most important user of the metal cutting machine tool and mold manufacturing industry. In terms of automotive parts processing, China's CNC lathes and vertical machining centers can basically meet the needs of auto parts mold manufacturing.
In addition, a number of sensors are used during the production of the machine tool, such as touch sensors for position detection, proximity switches, piezoelectric sensors for detecting pressure, piezoresistive sensors, and capacitive sensors, as well as common platinum sensors. Copper-based thermoelectric cathode sensors, semiconductor-based thermistor sensors and thermocouple sensors. On CNC machine tools, temperature sensors are used to detect temperature and compensate for overheating. The machine tool production process is based on sensors and other components. It also puts higher requirements on the sensors. The sensor expert network focuses on the connection between sensor technology and people's lives and provides a series of sensor solutions based on automotive electronics.
According to statistics, China's auto industry is currently the mainstay of machine tool consumption. Machine tools account for about two-thirds of the total investment in fixed assets of automobile manufacturers. Among them, the demand for machine parts for auto parts processing is about ten times larger than that for automakers. 70% of industry machine tool demand. Three years later, due to the large number of idle production capacity and large-scale mergers and reorganizations in China's auto industry, the demand for machine tools in China's auto processing industry will gradually decline, and its demand for machine tools will also be more environmentally friendly and efficient. The increase in demand for machine tools has further increased the requirements and quality requirements for various sensors such as proximity switches, speed sensors, and pressure sensors.
Thermoforming is a manufacturing process used to shape plastic sheets into various custom design products. It involves heating a plastic sheet until it becomes pliable, then using a mold or a vacuum to form it into the desired custom shape.
Thermoforming and vacuum forming are both processes used to shape plastic sheets into specific forms. However, there are some differences between the two techniques:
1. Process: In thermoforming, a plastic sheet is heated until it becomes pliable, and then it is pressed against a mold using pressure or a vacuum. Vacuum forming, on the other hand, relies solely on the use of a vacuum to draw the heated plastic sheet onto the mold.
2. Mold complexity: Thermoforming is typically used for more complex shapes and intricate molds, as it allows for greater detail and precision. Vacuum forming, on the other hand, is better suited for simpler shapes and molds that do not require as much detail.
3. Material thickness: Thermoforming is often used for thicker plastic sheets, typically ranging from 0.030 to 0.250 inches in thickness. Vacuum forming is more commonly used for thinner plastic sheets, typically ranging from 0.005 to 0.060 inches in thickness.
4. Production volume: Thermoforming is generally more suitable for high-volume production due to its faster cycle times and ability to handle larger sheets of plastic. Vacuum forming is better suited for low to medium volume production, as it has slower cycle times and is limited by the size of the vacuum forming machine.
5. Cost: Thermoforming typically requires more expensive equipment and molds, making it a more costly process compared to vacuum forming. Vacuum forming, on the other hand, is a more cost-effective option for smaller production runs or prototypes.
Overall, thermoforming is a more advanced and versatile process that offers greater precision and complexity, while vacuum forming is a simpler and more cost-effective option for less complex shapes and smaller production volumes.
Thermoforming is a versatile process that is widely used in industries such as packaging, automotive, aerospace, and medical. It offers advantages such as cost-effectiveness, quick turnaround times, and the ability to produce complex shapes with high precision.
Custom Thermoforming,Thermoforming Plastic Products,Thermoforming Process,ABS Thermoforming
Dongguan Yiyongli Industrial Co.,Ltd. , https://www.dgthermoforming.com